Descubre paso a paso cómo funciona un motor de corriente directa: todo lo que necesitas saber
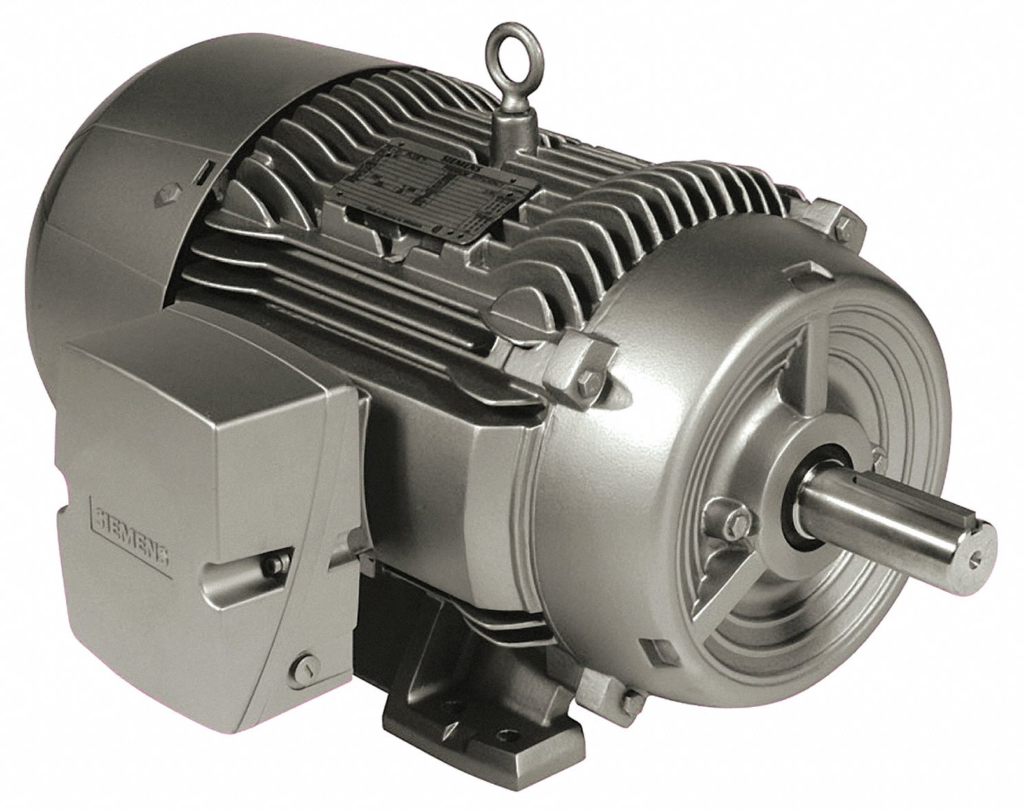
Un motor de corriente directa es un dispositivo que convierte la energía eléctrica en energía mecánica. Este tipo de motor es ampliamente utilizado en una variedad de aplicaciones, desde electrodomésticos hasta vehículos eléctricos. Comprender cómo funciona un motor de corriente directa es fundamental para poder sacarle el máximo provecho y realizar reparaciones cuando sea necesario.
Exploraremos paso a paso el funcionamiento de un motor de corriente directa. Primero, explicaremos los conceptos básicos de la corriente continua y cómo se genera el campo magnético necesario para que el motor funcione. A continuación, detallaremos la estructura interna de un motor de corriente directa y cómo se produce el movimiento rotatorio. Por último, analizaremos las diferentes configuraciones de conexiones y control de velocidad de un motor de corriente directa.
- Qué es un motor de corriente directa y cómo funciona
- Cuáles son las partes principales de un motor de corriente directa
- Cuál es el principio de funcionamiento de un motor de corriente directa
- Cómo se genera el campo magnético en un motor de corriente directa
- Qué es el conmutador y cuál es su función en un motor de corriente directa
- Qué diferencia hay entre un motor de corriente directa y un motor de corriente alterna
- Cuáles son las aplicaciones comunes de los motores de corriente directa
- Cuáles son las ventajas y desventajas de los motores de corriente directa
- Cómo se controla la velocidad de un motor de corriente directa
- Qué mantenimiento requiere un motor de corriente directa
-
Preguntas frecuentes (FAQ)
- 1. ¿Qué es un motor de corriente directa?
- 2. ¿Cuál es la diferencia entre un motor de corriente directa y un motor de corriente alterna?
- 3. ¿Cómo funciona un motor de corriente directa?
- 4. ¿Cuáles son las aplicaciones de los motores de corriente directa?
- 5. ¿Cuáles son las ventajas de utilizar un motor de corriente directa?
Qué es un motor de corriente directa y cómo funciona
Un motor de corriente directa es un dispositivo que convierte la energía eléctrica en energía mecánica, mediante la creación de un campo magnético. Este tipo de motor es ampliamente utilizado en diferentes dispositivos y aplicaciones, desde electrodomésticos hasta vehículos eléctricos.
Este tipo de motor se caracteriza por tener un par de polos magnéticos, uno positivo y otro negativo, que generan un campo magnético constante en su interior. Además, cuenta con un rotor que contiene bobinas o imanes permanentes que interactúan con el campo magnético generado, lo que produce un movimiento rotacional.
<p>
El funcionamiento de un motor de corriente directa se basa en dos principios fundamentales: la ley de Ampère y la ley de Faraday.
Ley de Ampère
La ley de Ampère establece que una corriente eléctrica que circula a través de un conductor produce un campo magnético a su alrededor. En el caso de un motor de corriente directa, este campo magnético es producido por los polos magnéticos.
Es importante destacar que estos polos magnéticos deben ser de polaridad opuesta para poder generar un campo magnético uniforme y constante. Esto se logra utilizando un sistema de escobillas y conmutadores que permiten invertir la dirección de la corriente eléctrica en las bobinas del rotor, manteniendo así la polaridad adecuada.
Ley de Faraday
La ley de Faraday establece que un conductor que se mueve dentro de un campo magnético experimenta una fuerza electromotriz, lo que a su vez genera una corriente eléctrica en el conductor. En el caso de un motor de corriente directa, esta corriente eléctrica es generada en las bobinas del rotor al interactuar con el campo magnético producido por los polos.
Esta corriente eléctrica, a su vez, genera un nuevo campo magnético que interactúa con el campo magnético generado por los polos, lo que produce un par de fuerzas que hacen girar el rotor y, por consiguiente, el eje del motor.
Una vez que se ha comprendido la base teórica del funcionamiento de un motor de corriente directa, resulta fascinante adentrarse en los detalles de su construcción y operación. En los próximos apartados, exploraremos paso a paso cada componente y proceso involucrado.
Cuáles son las partes principales de un motor de corriente directa
Un motor de corriente directa se compone de varias partes fundamentales que permiten su correcto funcionamiento. A continuación, te presentaremos las partes principales de un motor de corriente directa y cómo cada una de ellas contribuye a generar su movimiento.
1. Carcasa o estructura
La carcasa o estructura del motor de corriente directa es la parte externa que protege y alberga todas las demás partes internas. Suele estar fabricada de materiales resistentes como metal o plástico para garantizar la durabilidad y resistencia del motor.
2. Bobinas
Las bobinas son componentes esenciales en un motor de corriente directa. Están constituidas por alambres conductores enrollados en forma de espiral alrededor de un núcleo magnético. Estas bobinas generan el campo electromagnético que permite la rotación del motor.
3. Escobillas
Las escobillas son contactos eléctricos que se encuentran en contacto con las bobinas del rotor. Su función principal es establecer la conexión necesaria para transmitir la corriente eléctrica al rotor y así permitir su movimiento.
4. Rotor
El rotor es una de las partes móviles del motor de corriente directa. Generalmente está formado por un eje central y un conjunto de imanes permanentes. Cuando la corriente eléctrica circula por las bobinas del estator, se genera un campo magnético que interactúa con los imanes del rotor, lo que produce la rotación del motor.
5. Estator
El estator es otra de las partes fundamentales en un motor de corriente directa. Se trata de un conjunto de imanes fijos que rodean al rotor. Su función principal es generar el campo magnético necesario para impulsar la rotación del rotor cuando la corriente eléctrica circula por las bobinas.
6. Colector con anillos y delgas
El colector es un componente clave en los motores de corriente directa. Consiste en una serie de anillos y delgas de metal que se encuentran conectados a las bobinas del rotor. Su función es permitir el flujo de corriente entre las escobillas y el rotor, asegurando así su correcto funcionamiento.
7. Diodos rectificadores
En algunos motores de corriente directa, especialmente los utilizados en aplicaciones industriales, se pueden encontrar diodos rectificadores. Estos componentes son responsables de convertir la corriente alterna suministrada por la fuente de energía en corriente continua, necesaria para alimentar el motor.
8. Engranajes (en caso de motores de corriente directa con transmisión)
En algunos casos, los motores de corriente directa pueden contar con sistemas de transmisión que incluyen engranajes. Estos engranajes permiten adaptar la velocidad y/o el torque del motor a las necesidades específicas de cada aplicación.
Como puedes ver, un motor de corriente directa está compuesto por varias partes que trabajan en conjunto para generar el movimiento. Cada una de estas partes desempeña un papel fundamental en el funcionamiento del motor, desde la generación del campo magnético hasta la transmisión de la corriente eléctrica.
Cuál es el principio de funcionamiento de un motor de corriente directa
Un motor de corriente directa es un dispositivo electromecánico que convierte la energía eléctrica en energía mecánica. Su principio de funcionamiento se basa en la ley de Ampère y la ley de Faraday, que establecen que cuando una corriente eléctrica pasa a través de un conductor inmerso en un campo magnético, se generará un par de fuerzas que provocarán el movimiento del conductor.
En el caso de un motor de corriente directa, el campo magnético está generado generalmente por imanes permanentes o electroimanes, mientras que el conductor es una bobina que se encuentra montada sobre un eje. Al aplicar una corriente eléctrica a la bobina, esta se convierte en un imán temporal que interactúa con el campo magnético del motor.
La interacción entre el campo magnético y la corriente eléctrica generada en la bobina produce un par de fuerzas según la ley de Ampère, que hacen que la bobina comience a girar alrededor de su eje. A medida que la bobina gira, se genera una corriente inducida en ella, de acuerdo con la ley de Faraday, que a su vez produce un campo magnético opuesto al campo original. Este campo magnético inducido interactúa con el campo magnético del motor, generando un movimiento continuo.
Para que el motor de corriente directa funcione correctamente, es necesario contar con un sistema de conmutación que permita invertir el sentido de la corriente eléctrica en la bobina en el momento adecuado para mantener el movimiento constante. Esto se logra utilizando un conmutador o escobillas, que funcionan como interruptores mecánicos que cambian la dirección de la corriente eléctrica en la bobina cada vez que esta alcanza una posición específica.
Componentes principales de un motor de corriente directa
Un motor de corriente directa está compuesto por varios componentes principales que trabajan en conjunto para su correcto funcionamiento:
Bobina o devanado:
es la parte del motor que convierte la energía eléctrica en energía mecánica a través de sus interacciones con el campo magnético.Imanes permanentes o electroimanes:
generan el campo magnético necesario para que ocurra la interacción con la bobina y se produzca el movimiento.Eje:
permite que la bobina gire alrededor de él, transmitiendo el movimiento al sistema mecánico que se busca impulsar.Conmutador o escobillas:
son los encargados de invertir el sentido de la corriente eléctrica en la bobina en el momento adecuado para mantener el movimiento constante.Sistema de alimentación:
proporciona la corriente eléctrica necesaria para el funcionamiento del motor, ya sea a través de baterías, fuentes de alimentación o circuitos externos.
Estos componentes trabajan en conjunto para transformar la energía eléctrica en energía mecánica, permitiendo que los motores de corriente directa sean ampliamente utilizados en aplicaciones que requieren un control preciso del movimiento, como en robots, juguetes, vehículos eléctricos y muchas otras aplicaciones industriales.
Es importante mencionar que existen diferentes tipos de motores de corriente directa, como los motores de imán permanente, los motores sin escobillas (brushless) y los motores paso a paso, cada uno con características y aplicaciones específicas. Sin embargo, todos comparten el mismo principio básico de funcionamiento descrito anteriormente.
Cómo se genera el campo magnético en un motor de corriente directa
En un motor de corriente directa, el campo magnético se genera a través del uso de imanes permanentes o mediante el uso de electroimanes. Estos componentes son esenciales para el funcionamiento del motor y permiten la conversión de energía eléctrica en energía mecánica.
En el caso de los motores de corriente directa con imanes permanentes, estos están compuestos por imanes con polos norte y sur fijos en una disposición específica. El rotor del motor está equipado con bobinas que contienen conductores eléctricos. Cuando se aplica una corriente eléctrica a estas bobinas, se produce un flujo de corriente que genera un campo magnético alrededor de ellas.
Este campo magnético interactúa con los imanes permanentes del estator y crea una fuerza electromagnética que impulsa el movimiento del rotor. La dirección de la corriente eléctrica determina la polaridad magnética del campo generado por las bobinas, lo que hace que el rotor gire en una dirección específica.
En el caso de los motores de corriente directa con electroimanes, el campo magnético se genera mediante el uso de bobinas enrolladas alrededor del estator. Estas bobinas están conectadas a una fuente de corriente continua y actúan como electroimanes cuando circula la corriente a través de ellas.
Al igual que con los motores de imanes permanentes, el campo magnético generado por los electroimanes interactúa con los polos del rotor y genera una fuerza electromagnética que impulsa su movimiento. La ventaja de utilizar electroimanes en lugar de imanes permanentes es que la polaridad magnética se puede cambiar fácilmente al invertir la dirección de la corriente eléctrica, lo que permite un mayor control sobre el motor.
En un motor de corriente directa, el campo magnético se genera ya sea a través de imanes permanentes o mediante el uso de electroimanes. Este campo magnético interactúa con el rotor y genera una fuerza electromagnética que impulsa su movimiento. El funcionamiento preciso del motor depende de la correcta sincronización entre el campo magnético y el flujo de corriente eléctrica a través de las bobinas o los electroimanes.
Qué es el conmutador y cuál es su función en un motor de corriente directa
El conmutador es una parte fundamental en el funcionamiento de un motor de corriente directa. Se trata de un dispositivo mecánico que se utiliza para invertir la dirección del flujo de corriente en la armadura del motor, lo cual a su vez produce la rotación del mismo.
En un motor de corriente directa, la corriente eléctrica fluye tanto por las bobinas del stator como por la armadura o rotor. La función del conmutador es permitir que la corriente pase alternativamente a través de distintas partes de la armadura, generando así un campo magnético giratorio que impulsa la rotación del eje del motor.
El conmutador está compuesto por una serie de segmentos metálicos, llamados láminas, que están montados en un tambor aislante. Cada lámina se encuentra conectada individualmente a una de las bobinas de la armadura del motor. Además, en contacto con las láminas se encuentran las escobillas, unas piezas conductoras que permiten el paso de corriente hacia los segmentos del conmutador.
Cuando la corriente eléctrica fluye desde la fuente de alimentación al motor, las escobillas hacen contacto con las diferentes láminas del conmutador. A medida que el rotor gira dentro del estator, las láminas del conmutador se conectan y desconectan de forma secuencial con las escobillas, lo que cambia la dirección del flujo de corriente en la armadura, permitiendo así que el motor continúe girando constantemente.
Es importante destacar que el conmutador debe estar correctamente sincronizado con las bobinas del motor, de lo contrario, se puede producir un mal funcionamiento o incluso dañar el equipo. Por esta razón, es esencial llevar a cabo un adecuado mantenimiento y revisión periódica del conmutador para asegurarse de que esté en buen estado y cumpla su función correctamente.
Funcionamiento del conmutador en un motor de corriente directa
El funcionamiento del conmutador en un motor de corriente directa se basa en el principio de la conmutación electromecánica. Cuando la corriente eléctrica fluye hacia las bobinas de la armadura, las escobillas hacen contacto con una lámina del conmutador, permitiendo que la corriente circule a través de la bobina conectada a esa lámina en particular. A medida que el rotor gira, las láminas del conmutador se van conectando y desconectando rápidamente de las escobillas, haciendo que la corriente cambie de dirección en la armadura, generando así el campo magnético giratorio que impulsa la rotación del eje del motor.
El proceso de conmutación se repite continuamente durante el funcionamiento del motor, lo que garantiza que la corriente siempre fluya en la dirección adecuada para mantener la rotación constante del rotor. El conmutador actúa como un interruptor mecánico que cambia instantáneamente la ruta de la corriente en la armadura del motor, asegurando así la correcta operación del mismo.
El conmutador desempeña un papel crucial en el funcionamiento de un motor de corriente directa, al permitir la inversión del flujo de corriente en la armadura y generar el campo magnético necesario para la rotación del rotor. Su correcto mantenimiento y revisión periódica son fundamentales para garantizar un rendimiento óptimo y prolongar la vida útil del motor.
Qué diferencia hay entre un motor de corriente directa y un motor de corriente alterna
Antes de adentrarnos en los detalles de cómo funciona un motor de corriente directa, es importante entender la diferencia entre un motor de corriente directa (DC) y un motor de corriente alterna (AC).
En primer lugar, la principal diferencia radica en el tipo de corriente que utilizan para generar movimiento. Un motor de corriente directa utiliza corriente continua, lo que significa que la dirección de la corriente no cambia con el tiempo. Por otro lado, un motor de corriente alterna utiliza corriente alterna, que cambia su dirección periódicamente.
Otra diferencia importante está en la forma en que están construidos ambos motores. Los motores de corriente directa generalmente tienen un diseño más simple y menos partes móviles en comparación con los motores de corriente alterna. Esto los hace más adecuados para aplicaciones que requieren un control preciso de velocidad y torque.
Además, los motores de corriente directa son altamente eficientes en términos de conversión de energía eléctrica en movimiento mecánico. La corriente continua permite un flujo constante de energía a través del motor, lo que resulta en una mayor eficiencia energética.
Ventajas y desventajas de los motores de corriente directa
- Ventajas:
- Control preciso de velocidad y torque: Los motores de corriente directa permiten un control fino de la velocidad y el torque, lo que los hace ideales para aplicaciones que requieren un movimiento preciso.
- Arranque suave: Los motores de corriente directa tienen la capacidad de arrancar suavemente, evitando así sobrecargas en el sistema eléctrico.
- Alta eficiencia: Gracias a la corriente continua, estos motores son altamente eficientes en términos de conversión de energía eléctrica en movimiento mecánico.
- Desventajas:
- Mayor costo inicial: En comparación con los motores de corriente alterna, los motores de corriente directa tienden a ser más costosos desde el punto de vista económico.
- Mantenimiento requerido: Estos motores necesitan un mantenimiento adecuado para asegurar un funcionamiento óptimo a lo largo del tiempo.
- Limitaciones de potencia: Aunque los motores de corriente directa son eficientes, tienen limitaciones en cuanto a su potencia máxima.
A pesar de las diferencias y las características particulares de los motores de corriente directa, su uso es amplio en una variedad de aplicaciones, desde pequeños electrodomésticos hasta vehículos eléctricos.
Cuáles son las aplicaciones comunes de los motores de corriente directa
Los motores de corriente directa son ampliamente utilizados en una variedad de aplicaciones en diferentes industrias. Su capacidad para convertir la energía eléctrica en movimiento mecánico los hace ideales para muchas tareas y procesos. A continuación, te presentamos algunas de las aplicaciones más comunes de los motores de corriente directa:
1. Automatización industrial
Los motores de corriente directa se utilizan extensivamente en la automatización industrial. Estos motores son utilizados en maquinarias y equipos que realizan tareas repetitivas y precisas, como robots industriales, cintas transportadoras y sistemas de manipulación de materiales.
2. Ventiladores y compresores
Los motores de corriente directa también se utilizan en ventiladores y compresores. Estos motores son ideales para este tipo de aplicaciones debido a su alto par de arranque y su capacidad para mantener una velocidad constante incluso bajo condiciones variables de carga.
3. Vehículos eléctricos
Con el creciente interés en los vehículos eléctricos, los motores de corriente directa han ganado popularidad. Estos motores son ideales para vehículos eléctricos debido a su alta eficiencia y su capacidad para proporcionar un torque instantáneo, lo que permite una aceleración rápida y respuesta inmediata al pedal del acelerador.
4. Aplicaciones marinas
Los motores de corriente directa también se utilizan en aplicaciones marinas, como embarcaciones y submarinos. Estos motores son ampliamente utilizados debido a su capacidad para trabajar en ambientes húmedos y salinos, así como su alta confiabilidad y resistencia a las vibraciones.
5. Tecnología médica
Los motores de corriente directa también se utilizan en la tecnología médica, especialmente en equipos y dispositivos que requieren un control preciso del movimiento, como bombas de infusión, equipos de diálisis y sistemas de producción de imágenes médicas.
6. Electrodomésticos
En el ámbito de los electrodomésticos, los motores de corriente directa se encuentran en aplicaciones como lavadoras, secadoras y extractores de cocina. Estos motores ofrecen un rendimiento eficiente y un funcionamiento silencioso, lo que los hace ideales para su uso en hogares.
7. Energía renovable
En el campo de la energía renovable, los motores de corriente directa se utilizan en turbinas eólicas y sistemas solares fotovoltaicos. Estos motores ayudan a convertir la energía renovable en electricidad utilizable al generar el movimiento necesario para capturar y almacenar energía.
Estas son solo algunas de las aplicaciones comunes de los motores de corriente directa. Su versatilidad y eficiencia los convierten en una opción popular en muchas industrias y sectores. Los motores de corriente directa son fundamentales para impulsar el progreso y la innovación en diversos campos y continuarán desempeñando un papel clave en el futuro.
Cuáles son las ventajas y desventajas de los motores de corriente directa
Los motores de corriente directa son una tecnología ampliamente utilizada en diversas aplicaciones industriales y comerciales. Tienen muchas ventajas, pero también presentan algunas desventajas que es importante considerar. En esta sección, exploraremos cuáles son estas ventajas y desventajas.
Ventajas de los motores de corriente directa
- Control de velocidad preciso: Una de las principales ventajas de los motores de corriente directa es su capacidad para proporcionar un control de velocidad altamente preciso. Esto se logra ajustando la tensión o la corriente suministrada al motor. Esta característica es especialmente útil en aplicaciones donde se requiere un control fino de la velocidad, como en máquinas herramientas, robots y sistemas de transporte automatizados.
- Arranque suave: Los motores de corriente directa ofrecen la posibilidad de un arranque suave, lo que significa que pueden acelerar gradualmente desde el reposo hasta la velocidad deseada. Este tipo de arranque es ideal para evitar daños al motor y al sistema mecánico asociado. Además, el arranque suave también puede ayudar a reducir las sobretensiones y las picos de corriente durante el proceso de encendido.
- Elevado par de arranque: Otra ventaja importante de los motores de corriente directa es su capacidad para proporcionar un elevado par de arranque. Esto significa que son capaces de generar un alto nivel de fuerza inicial al momento de arrancar. Esta característica es especialmente beneficiosa en aplicaciones donde se requiere una gran potencia de arranque, como en ascensores y grúas.
- Compactos y livianos: Los motores de corriente directa tienden a ser más compactos y livianos en comparación con otros tipos de motores. Esto los hace ideales para aplicaciones que requieren un diseño compacto y una alta densidad de potencia, como en vehículos eléctricos y dispositivos portátiles.
Desventajas de los motores de corriente directa
- Costo: Aunque los motores de corriente directa son ampliamente utilizados y tienen muchas ventajas, suelen ser más costosos que otros tipos de motores, lo cual puede representar un obstáculo en ciertos proyectos o aplicaciones con presupuestos limitados.
- Mantenimiento: Los motores de corriente directa requieren un mantenimiento regular para garantizar su correcto funcionamiento a largo plazo. Esto implica labores de limpieza, lubricación y revisión periódica de los componentes, lo que puede resultar en mayores costos y tiempo dedicado al mantenimiento.
- Escobillas y desgaste mecánico: En los motores de corriente directa, las escobillas son componentes clave que permiten la conexión entre el rotor y el estator. Sin embargo, estas escobillas están sujetas a desgaste mecánico debido a la fricción constante. Con el tiempo, las escobillas pueden desgastarse y necesitar ser reemplazadas, lo que implica costos adicionales y tiempo de inactividad en el sistema.
- Control de ruido y vibraciones: Los motores de corriente directa pueden generar ruido y vibraciones durante su funcionamiento. Esto puede ser problemático en ciertas aplicaciones donde se requiere un funcionamiento silencioso o una reducción de las vibraciones, como en equipos electrónicos sensibles o en entornos donde el ruido es un factor crítico.
Los motores de corriente directa tienen varias ventajas significativas, como un control de velocidad preciso, arranque suave, elevado par de arranque y un diseño compacto y liviano. Sin embargo, también presentan algunas desventajas, como un costo inicial más alto, necesidad de mantenimiento regular, desgaste mecánico de las escobillas y posibles problemas de ruido y vibraciones. Al considerar la elección de un motor para una aplicación específica, es importante analizar cuidadosamente estas ventajas y desventajas y evaluar qué características son más relevantes para cumplir con los requisitos del proyecto.
Cómo se controla la velocidad de un motor de corriente directa
El control de velocidad en un motor de corriente directa es fundamental para su correcto funcionamiento y para adaptarlo a diversas aplicaciones en las que se requiera un rango variable de velocidades. Existen diferentes métodos para controlar la velocidad de un motor de corriente directa, cada uno con sus ventajas y desventajas.
Control de velocidad por voltaje
Una forma común de controlar la velocidad de un motor de corriente directa es mediante el control de voltaje aplicado al motor. Cuanto mayor sea el voltaje suministrado al motor, mayor será la velocidad. Esto se debe a que el voltaje determina la fuerza electromotriz que impulsa al motor a girar.
Para controlar la velocidad mediante el voltaje, se utilizan resistencias variables o dispositivos electrónicos como los transistores de potencia. Estos componentes permiten regular el voltaje suministrado al motor, lo que a su vez regula la velocidad de giro.
Control de velocidad por cambio de voltaje de campo
Otro método para controlar la velocidad de un motor de corriente directa es mediante el cambio del voltaje de campo. El voltaje de campo es aquel que se aplica al devanado de campo del motor, y su variación influye directamente en la velocidad de giro del rotor.
Al modificar el voltaje de campo, se altera la fuerza magnetomotriz generada en el motor, lo que a su vez afecta la velocidad. Este método de control puede ser más eficiente en determinadas aplicaciones, ya que permite un mayor rango de velocidades ajustables.
Control de velocidad por modulación de ancho de pulso (PWM)
La modulación de ancho de pulso, o PWM por sus siglas en inglés (Pulse Width Modulation), es una técnica ampliamente utilizada para controlar la velocidad de los motores de corriente directa. Consiste en variar el ancho del pulso de tensión aplicado al motor, manteniendo constante el voltaje.
Este método es especialmente utilizado en controladores electrónicos modernos, donde se generan pulsos de tensión que pueden variar rápidamente en anchura. Cuanto mayor sea el ancho del pulso, mayor será la velocidad del motor, mientras que un pulso más estrecho reducirá la velocidad.
Control de velocidad por realimentación
Un último método utilizado para controlar la velocidad de un motor de corriente directa es mediante sistemas de realimentación o retroalimentación. Estos sistemas consisten en sensores que captan la velocidad actual del motor y la comparan con la velocidad deseada preestablecida.
En función de esta comparación, se ajusta el controlador en tiempo real para mantener la velocidad del motor en el valor deseado. Entre los tipos de sensores utilizados para la realimentación se encuentran los encoders, que proporcionan información precisa sobre la velocidad y posición del rotor.
El control de velocidad en los motores de corriente directa es crucial para adaptar su funcionamiento a diversas aplicaciones. Los métodos mencionados, como el control por voltaje, cambio de voltaje de campo, modulación de ancho de pulso y realimentación, son solo algunas de las opciones disponibles. La elección del método dependerá de las necesidades específicas de cada aplicación.
Qué mantenimiento requiere un motor de corriente directa
El mantenimiento de un motor de corriente directa es fundamental para garantizar su correcto funcionamiento y prolongar su vida útil. Aunque estos motores son conocidos por ser robustos y fiables, requieren de ciertos cuidados y revisiones periódicas.
Uno de los aspectos más importantes en el mantenimiento de un motor de corriente directa es la limpieza regular de sus componentes. Esto incluye tanto el exterior del motor como las partes internas. Es recomendable utilizar un paño suave y seco para eliminar el polvo y la suciedad acumulada. Además, se debe prestar especial atención a la limpieza de las escobillas y los colectores, ya que estas piezas tienden a desgastarse con el uso y pueden afectar el rendimiento del motor si no se mantienen en buen estado.
Otro punto clave en el mantenimiento de un motor de corriente directa es la lubricación adecuada. Es importante revisar y, de ser necesario, reemplazar el aceite utilizado para lubricar los rodamientos y engranajes del motor. Un exceso de lubricante puede causar fricción y sobrecalentamiento, mientras que una falta de lubricación puede generar desgaste prematuro de las piezas. Se recomienda utilizar un lubricante de calidad y seguir las indicaciones del fabricante para realizar el mantenimiento adecuado.
Revisiones periódicas
Además de la limpieza y la lubricación, es necesario realizar revisiones periódicas al motor de corriente directa. Estas revisiones deben llevarse a cabo siguiendo las recomendaciones del fabricante y pueden incluir la comprobación de los niveles de tensión, el estado de los cables y conectores, así como la verificación del funcionamiento de los sensores y las protecciones eléctricas.
Es importante destacar que las revisiones periódicas deben ser realizadas por personal cualificado y utilizando las herramientas adecuadas. En caso de detectar algún problema o fallo en el motor, es fundamental actuar de manera inmediata para evitar daños mayores o accidentes.
Prevención de averías
Además del mantenimiento regular, existen algunas medidas que se pueden tomar para prevenir averías en un motor de corriente directa. Una de ellas es evitar la sobrecarga del motor, es decir, no exceder su capacidad máxima de trabajo. Esto puede ocasionar un calentamiento excesivo y provocar daños en el sistema.
Otra medida preventiva es asegurarse de que el motor esté instalado correctamente y que todos los componentes estén ajustados de forma adecuada. También es recomendable utilizar protecciones adicionales, como fusibles o interruptores de seguridad, para evitar sobrecargas o cortocircuitos.
El mantenimiento de un motor de corriente directa es fundamental para garantizar su buen funcionamiento y prolongar su vida útil. La limpieza regular, la lubricación adecuada y las revisiones periódicas son aspectos clave que deben ser tenidos en cuenta. Además, es importante tomar medidas preventivas para evitar averías y daños en el motor. Con un correcto mantenimiento, un motor de corriente directa puede proporcionar un rendimiento óptimo durante muchos años.
Preguntas frecuentes (FAQ)
1. ¿Qué es un motor de corriente directa?
Un motor de corriente directa es un dispositivo que convierte la energía eléctrica en energía mecánica mediante el uso de campos magnéticos.
2. ¿Cuál es la diferencia entre un motor de corriente directa y un motor de corriente alterna?
A diferencia de los motores de corriente alterna, los motores de corriente directa funcionan con una sola dirección de flujo de corriente, lo que les permite controlar la velocidad y el sentido de rotación de manera más precisa.
3. ¿Cómo funciona un motor de corriente directa?
Un motor de corriente directa utiliza un electroimán llamado rotor y un campo magnético fijo llamado estator. La corriente eléctrica fluye a través del rotor, creando un campo magnético que interactúa con el campo del estator para generar movimiento.
4. ¿Cuáles son las aplicaciones de los motores de corriente directa?
Los motores de corriente directa se utilizan en una amplia variedad de aplicaciones, como automóviles eléctricos, electrodomésticos, sistemas de automatización industrial y juguetes electrónicos.
5. ¿Cuáles son las ventajas de utilizar un motor de corriente directa?
Las ventajas de los motores de corriente directa incluyen un mayor control de la velocidad y el sentido de rotación, un alto par de arranque, una respuesta rápida y una mayor eficiencia energética en comparación con otros tipos de motores.
Deja una respuesta
Entradas relacionadas